Welcome to the Speed Shop
For all things wheel speed related
I wanted to find a reluctance ring that would provide the ECU with accurate wheel speeds, and after trying several OEM parts, decided to have a go at making my own. Drawn in Fusion 360, I use a UK based company to laser cut the rings to my design, and they can be seen on several race cars in the British Sprint paddock. Customers include SBD Motorsport, and both British Sprint Championship winning cars in 2022 and 2023. In 2024 I moved to 3D printing the speed sensor rings, with incredible success. This page explains the process involved in measuring wheel speed, and shows some of the parts I've made for other people. If you have a requirement, please get in touch. I'm sure I can help.How to get in touch
Please get in touch for prices and availability. Either contact me through my Facebook page, or send me an email to [email protected]Ebay shop
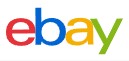
Reliable NPN 12V Barrel Sensor
I can supply NPN 12 Volt barrel induction sensors, to go with all the reluctance rings. They work at up to 4000 pulses per second (4KHz) switching frequency, and feature a bright internal LED to aid setting up. Prices start from £25 each. For best results, an induction sensor needs to be positioned with a gap between 1mm and 2mm to the reluctance ring tooth.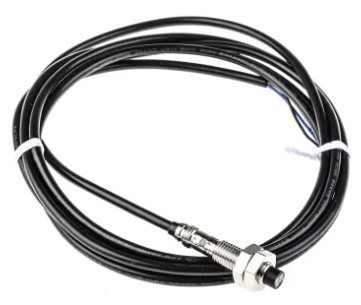
Switching frequency
How many pulses a second will a 20 tooth ring produce?On a car travelling at 150 mph, using a 13 inch 250/575 rear tyre, a tyre will rotate at 2227rpm, a 20 tooth ring will produce 742 pulses per second, and the car will travel 3.6" per pulse. With an older ECU, where the input frequency may be limited, we can produce a ring with fewer teeth to suit. For example a 12 tooth ring will produce 445 pulses per second at 150 mph, and the car will travel 5.9" per pulse.
Teeth | Pulses per second |
Distance per pulse |
---|---|---|
12 | 445 | 5.9" |
14 | 519 | 5.1" |
16 | 593 | 4.4" |
18 | 668 | 4.0" |
20 | 742 | 3.6" |
Laser cut steel rings
All the reluctance rings are designed to be a friction fit over the output cup, and are laser cut from 4, 5 or 6mm mild steel, in the UK. The design allows the ring to flex a little, so they are easy to fit, without the need for a hydraulic press. You can if you wish, loctite them in to position, though I've not had any issues with them moving in the three years I've been running them on my car.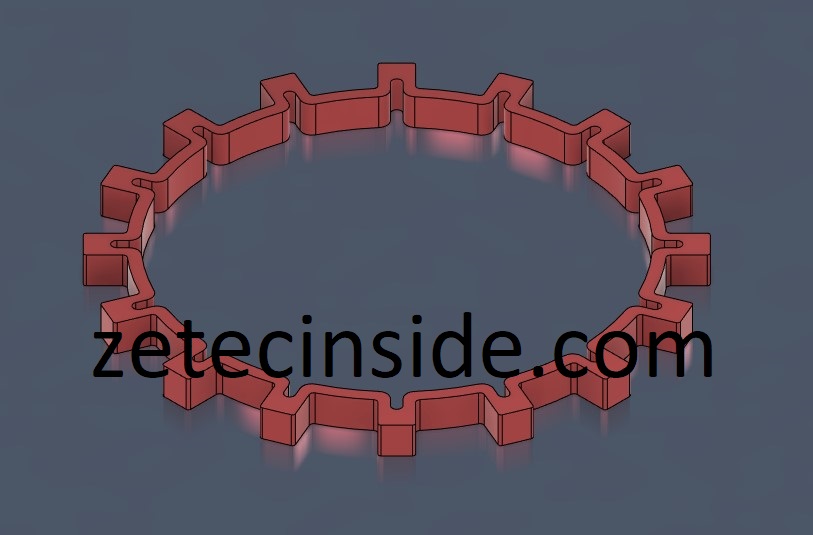
Hewland FTR fit reluctance ring
£40.00
Above is the 16-tooth Hewland FTR reluctance ring that I run on my Mygale EcoBoost. Laser cut in the UK from 6mm steel. The design allows a small amount of flex, which allows the rings to be friction fitted over the Hewland FTR output cup by gently drifting them on.
Each 7mm tall tooth provides a 36mm² surface to the sensor.
Weight: 54 grammes
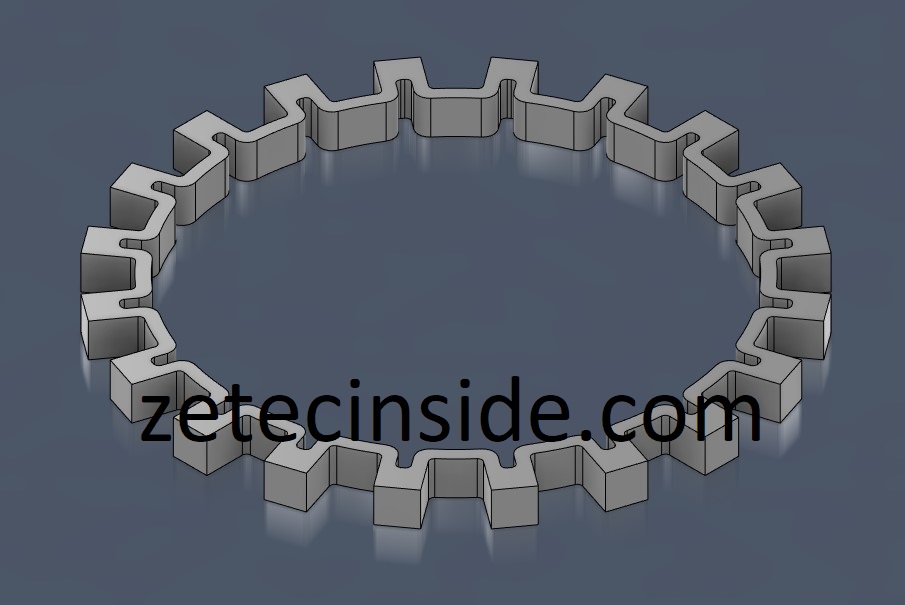
Empire EVO 2 reluctance ring
£40.00
Above is a 20-tooth reluctance ring for the Empire Evo 2.
This is a render of the output cup from the Empire Evo2, with the 20 tooth reluctance ring fitted. Drawn in Autodesk Fusion.
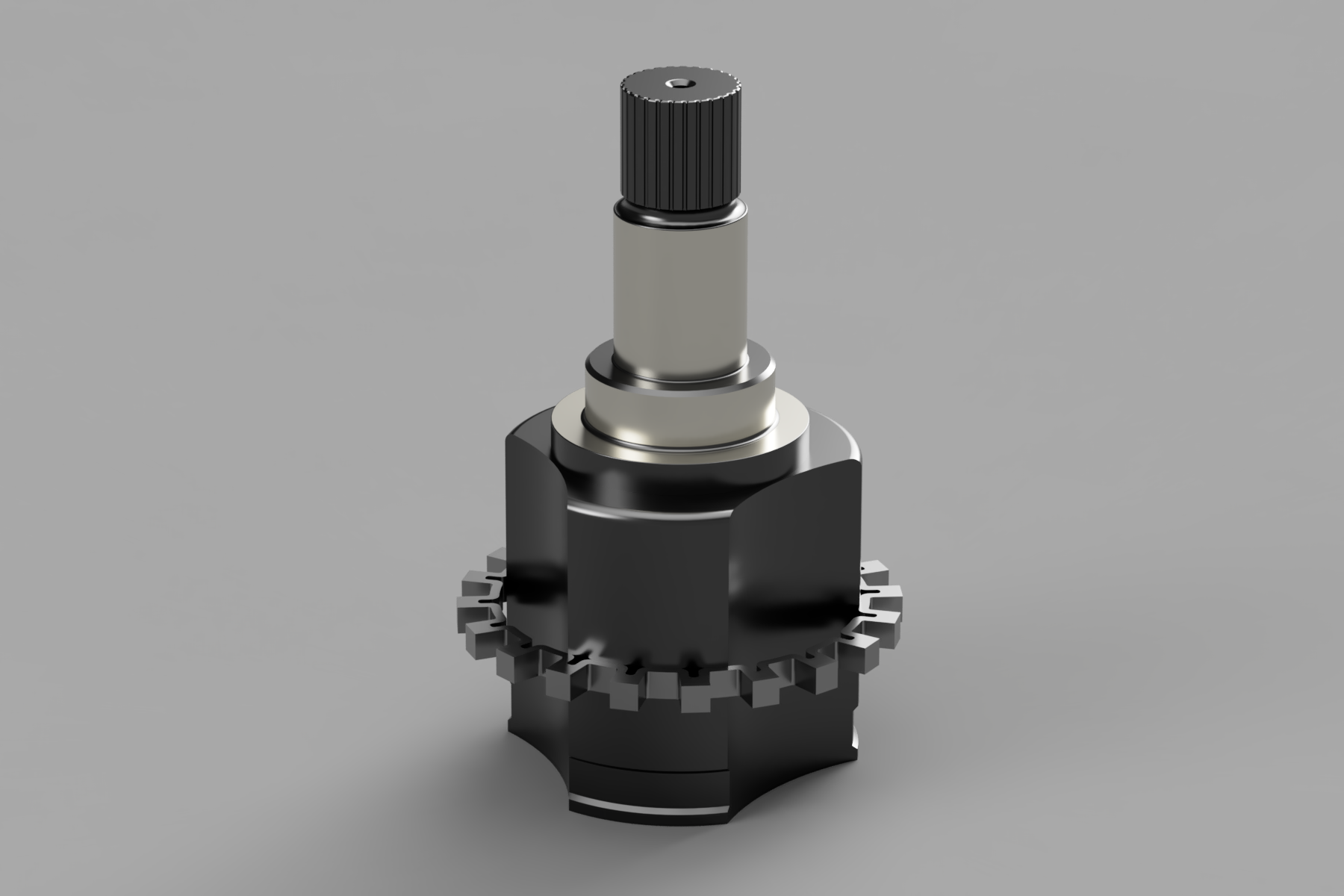
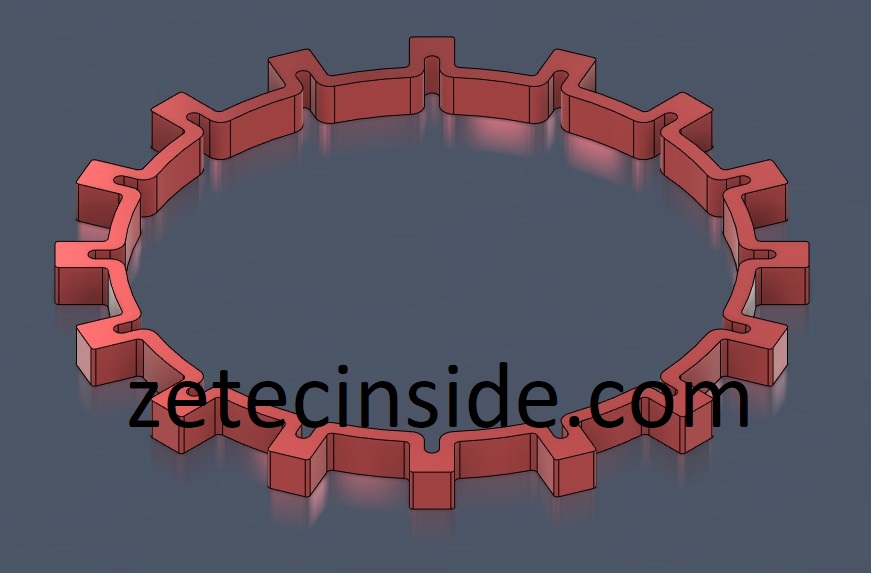
Ford Focus reluctance ring
£40.00
Above is a 16-tooth reluctance ring for the Ford Focus.

Force TA reluctance ring
£40.00
Above is a 16-tooth reluctance ring for the Force TA.
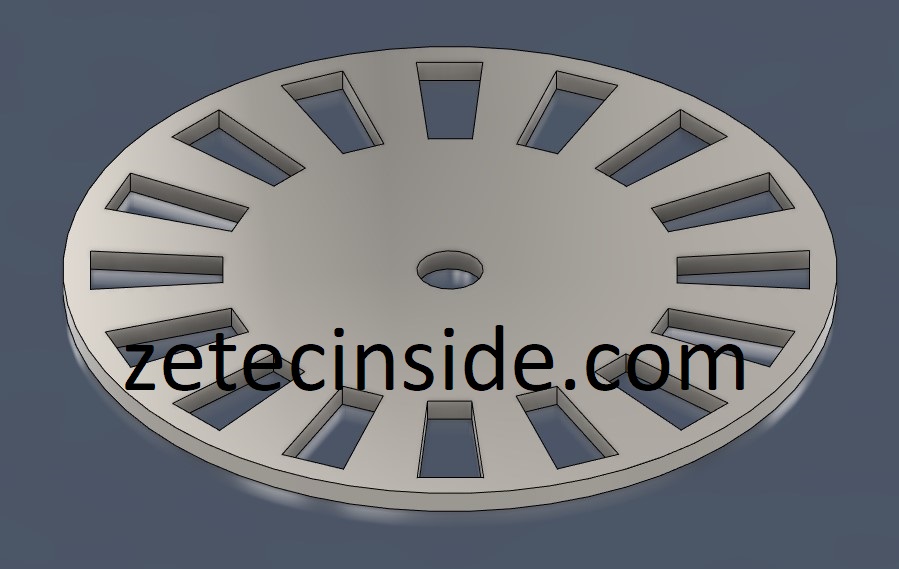
Front wheel trigger disk
£25.00
This is a 16-hole front wheel trigger disk, laser cut from 2mm steel.
70mm OD
6mm mounting hole
Weight: 40.5 grammes
RLM Atomic Racing Cup Car
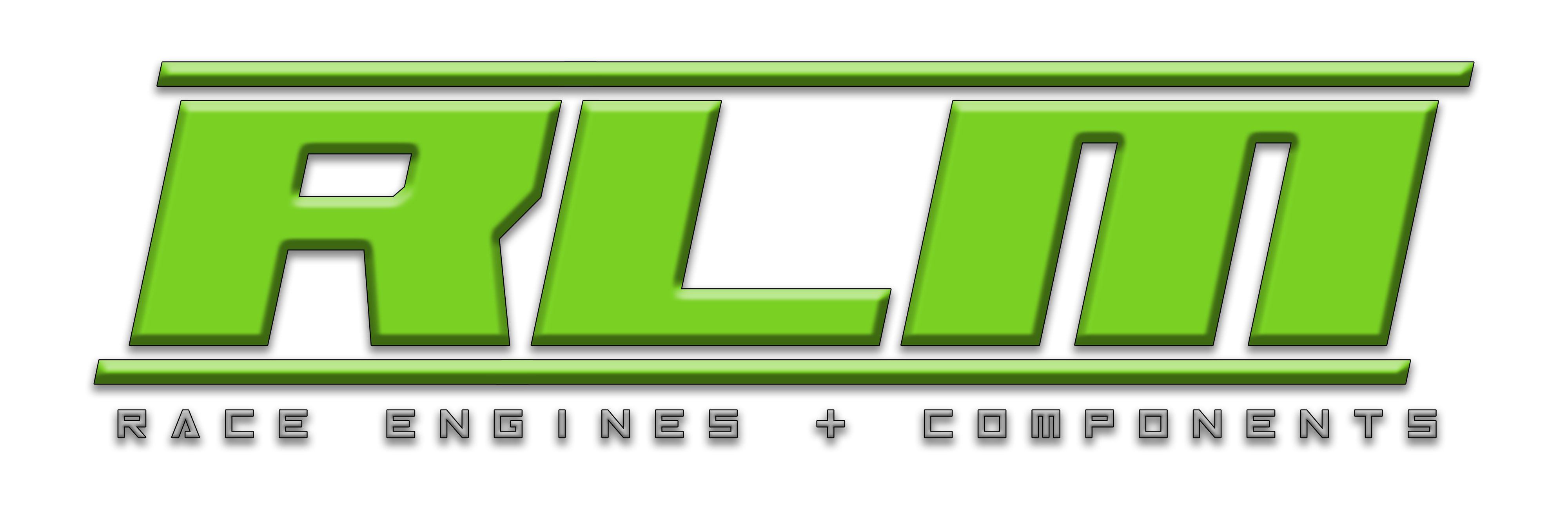
In February 2024 I was approached by RLM to design a Factory solution for the MK Cup 200 car, to allow them to run front and rear wheel speed sensors, so they could offer launch and traction control to their growing fleet of customer cars. I was loaned several parts, including a front hub assembly, which I modelled in Fusion to allow me to come up with a solution. I was also tasked with designing a folded steel bracket to position the barrel sensor adjacent to the trigger ring on the front hub.
Here is a video of the final solution for the front axle.
New for 2024: Printed front and rear trigger disks
Why 3D print
The prices for laser cutting small volume parts is simply astronomical at the moment. I was recently quoted over £400.00 for four reluctance rings. The science of 3D printing parts has moved on so far in the last 10 years, that the quality of the products has to be seen to be believed. My only reservation with using plastic is robustness, and its suitability for the front brakes where there is heat radiating from the brake disks. If you can manage those two factors, then 3D printed rings are definitely suitable.I use 4mm steel dowels for the induction sensors to detect rotation. The dowels are pressed in to the plastic rings, and are impossible to remove without using significant force. So they cannot fall out when the axle is rotating. I can design for radial or axial fitment of the steel dowels, you need to decide which is easiest for the mounting of the movement sensor.
Front axle
I have been testing with success, 3D SLS printed Nlyon front wheel trigger disks with axial dowels. These are printed in the UK on ProX 6100 printers, which produce the best quality SLS 3D prints on the market. Using 4mm steel dowels, these provide the ferrous material that the proximity sensor requires to measure rotation. On the front axle on my Mygale, I have been running a 20 dowel disk with no issues at all. Based on that success, I have now designed printed trigger disks for the Hewland FTR output cup, with an increasing number of dowels which were tested during my 2024 sprint season.For the front axle, the sensor is fitted at 90° to the disk, so the dowels are fitted at right angles to the sensor. This is the axial mount.
I have captured the signal from the sensor with the front wheel turning on the bench, at the equivalent of 300 mph.
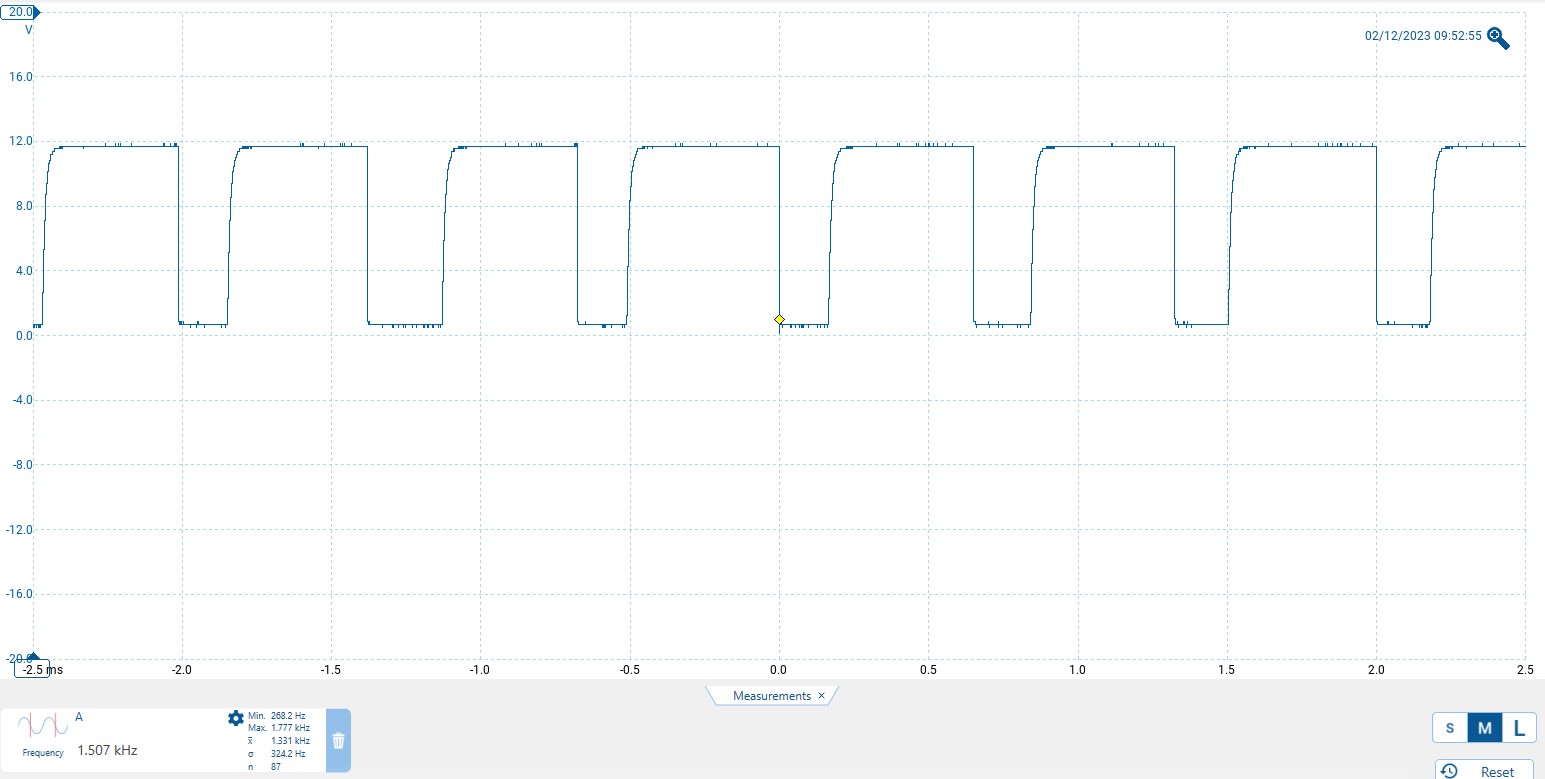
The trigger disk is printed from PA12 Nylon by 3D People, to my design, drawn in Fusion 360. The steel dowels are a press fit in to the holes in the disk.
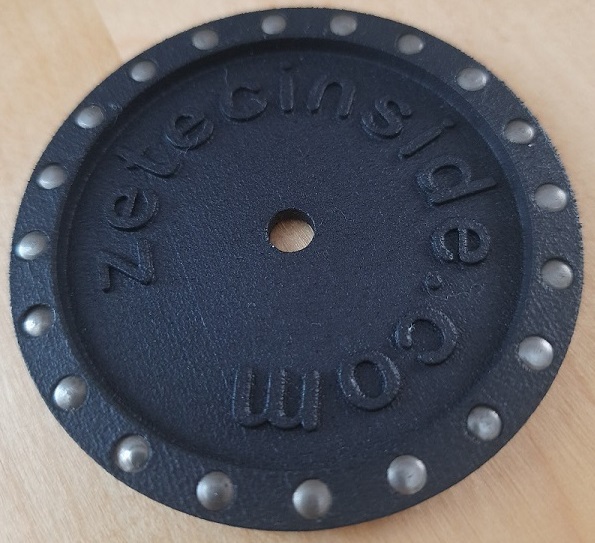
Rear axle
This is the axial 20 dowel disk, fitted to my Hewland FTR gearbox. I have designed varying numbers of dowels which will be tested over the 2024 season. The GT101 sensor is NLA, but there are copies on ebay which I'm told work just as well. In 2024 I tested a 37 dowel ring with no issues whatsoever.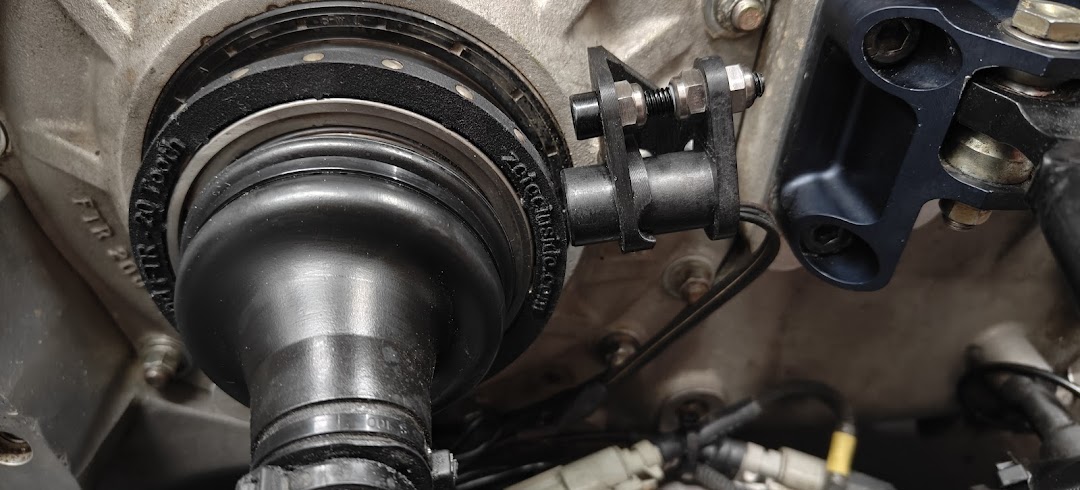
CAD renders of the range of rings that are going to be tested this year. They have 22, 24, 26, 28 and 30 holes for 4mm steel dowels.
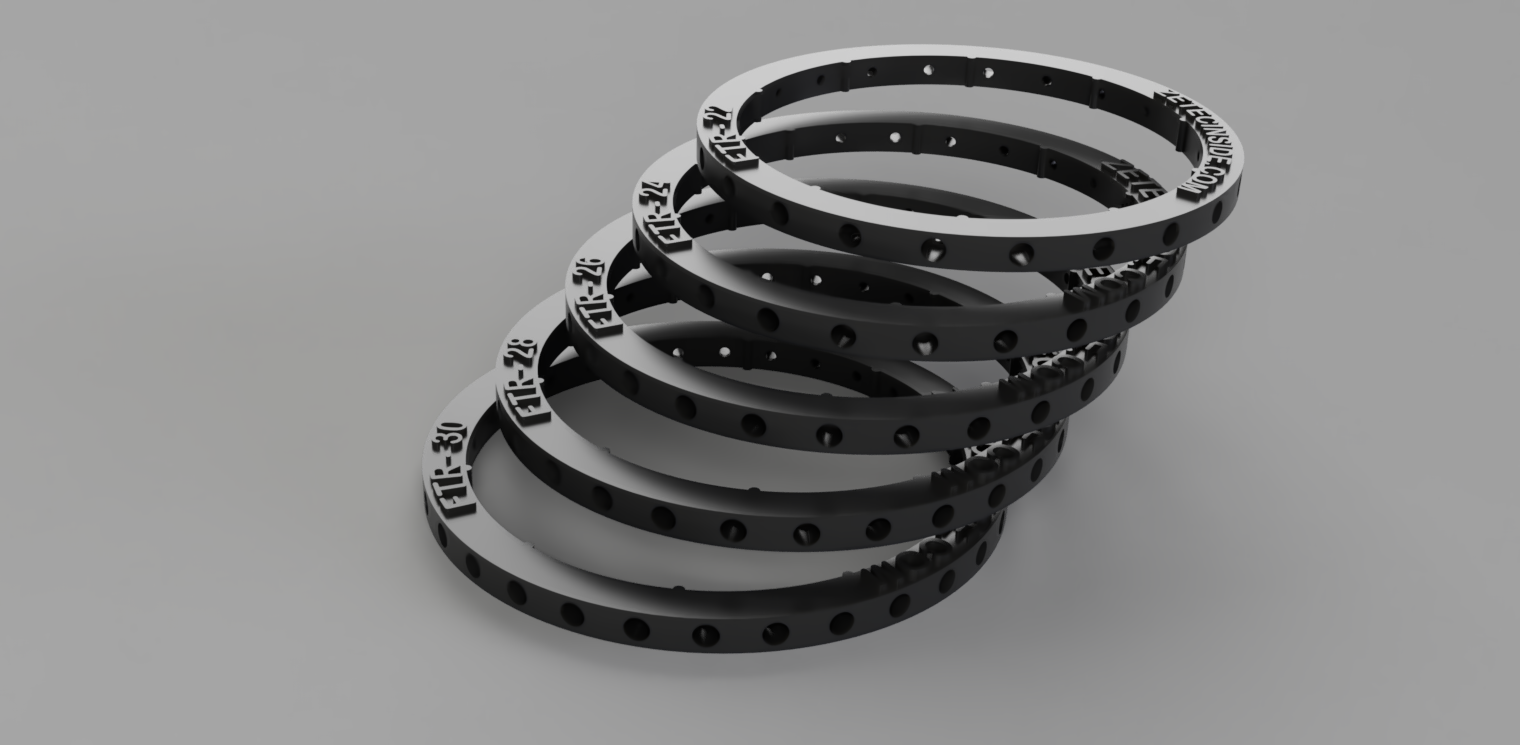
CAD images of the GT101 sensor fitted to the 3D printed Nylon mount
Sierra Differential speed sensor ring and sensor bracket
The Ford Sierra Differential Housing is synonymous with so many different home and factory built specials, that it made perfect sense to design a speed sensor ring and sensor bracket to allow NPN barrels sensors to be fitted, for traction and launch control. Working with a kit car owner, I designed the sensor ring to hold 37 steel dowels, and together we devised a way to support a simple printed bracket to suspend the NPN speed sensor above the printed ring. The sensor ring has an ID of 78mm and is a friction fit over the Sierra Push Fit output cup. A 50mm allen key stud M8x1.25 is screwed in to the differential housing, and a slim locknut is used to locate the metal tab. A second slim locknut is then used to lock the printed sensor bracket in place. The NPN speed sensor is then fitted to the bracket, positioning the tip of the sensor 1-2mm above the height of the printed sensor ring. The radial ring is a friction fit over the output cup, and can be secured with a smear of tigerseal sealant.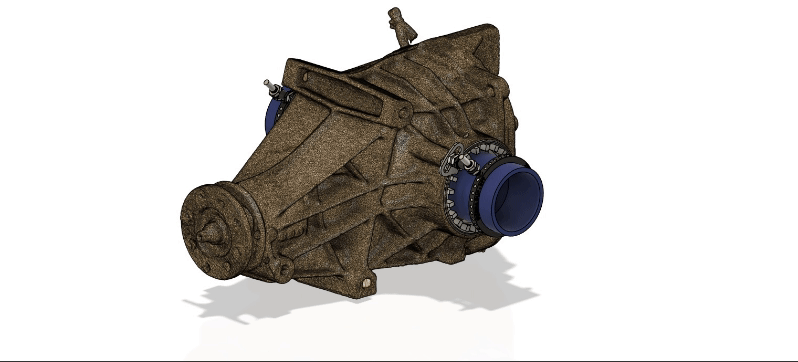
Animation of the Sierra sensor rings in action.
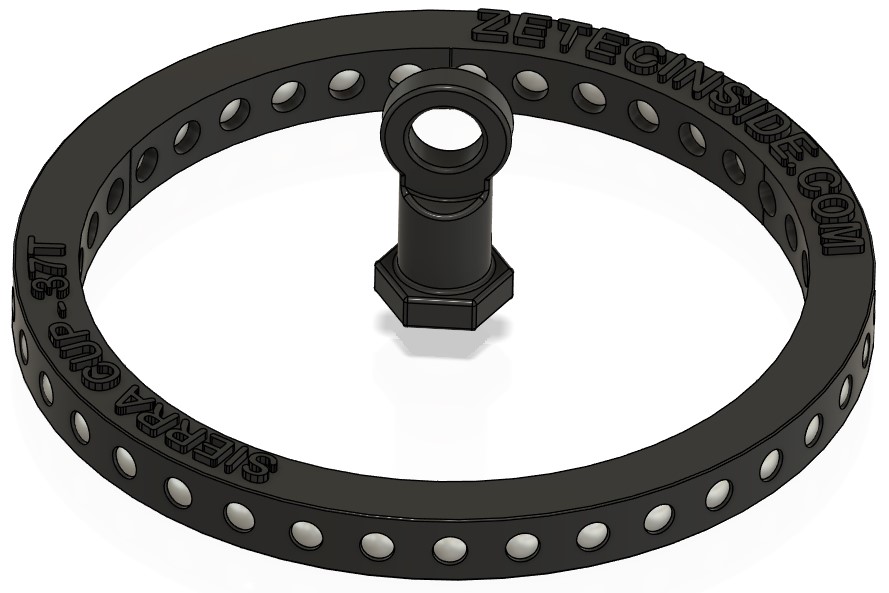
The radial Sierra rings are £35 each, complete with 37 steel 4mm dowels. Printed in Nylon PA12 SLS, with a black finish.
The printed Sierra sensor brackets are £5 each, suitable for the M8 NPN speed sensor, also printed in Nylon PA12 SLS, with a black dyed finish.
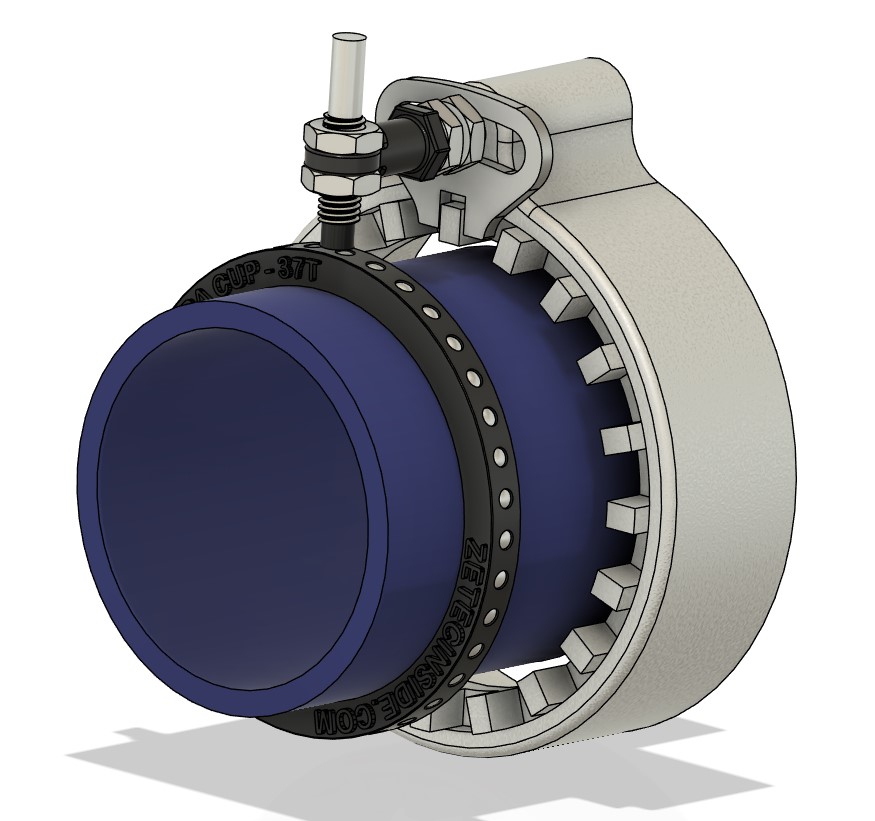
Computer model of the sensor ring and sensor bracket fitted to the Sierra Differential housing
Ariel Atom speed sensor ring
This is designed for the 91mm OD output cup, the rings feature 37 steel dowels, and are a friction fit over the output cup.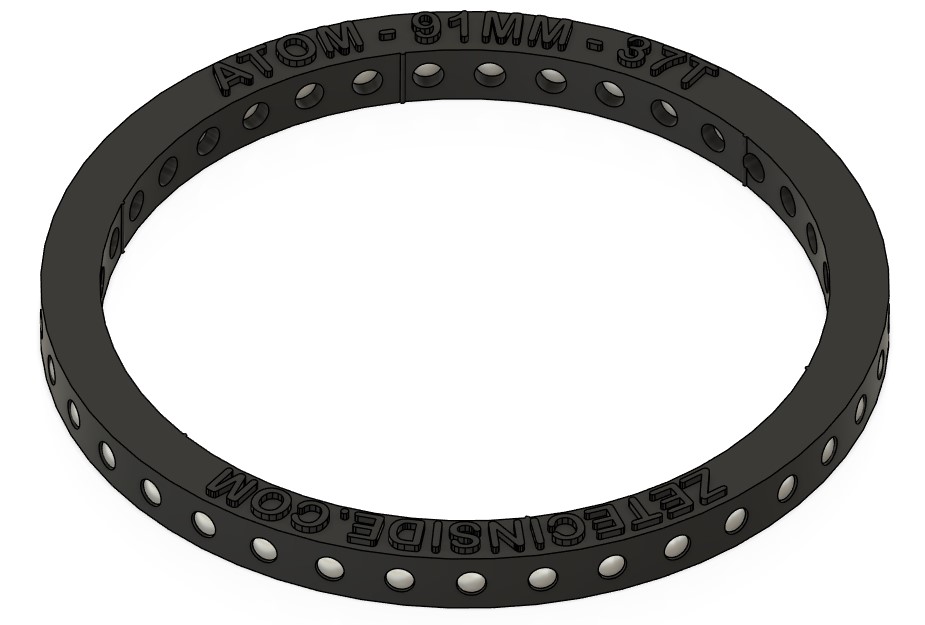
The radial Atom rings are £35 each, complete with 37 steel 4mm dowels. Printed in Nylon PA12 SLS, with a black finish.
Steel Ring Installation
On my car, the steel FTR reluctance rings are matched with Honeywell GT101 induction sensors, which are held on the gearbox using my 3D printed GT101 sensor brackets. The printed bracket uses an aluminium socket head M6x35mm bolt and titanium locknuts, to allow the sensor gap to be easily adjusted. In testing, this setup has proved 100% reliable, with zero speed drop outs, set using a ~2mm tooth gap. Using 16 teeth gives the ECU a high resolution, and the GT101 sensors work well with the 36mm⊃2 surface area of the teeth.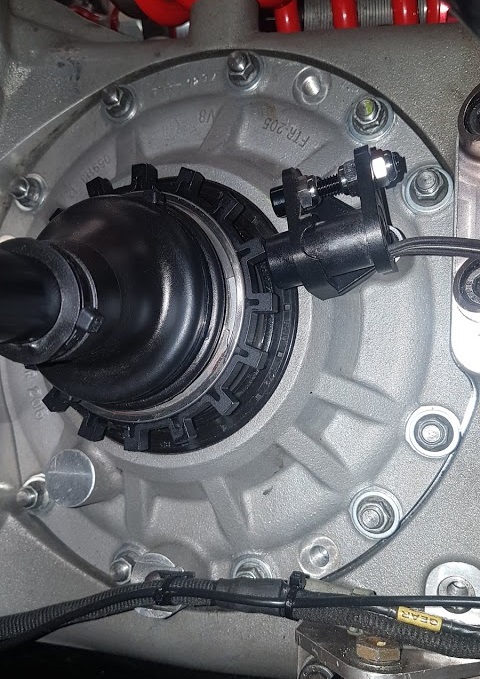